Search
Materials and Coatings

Advanced Materials for Electronics Insulation
Many researchers have attempted to use polymer-ceramic composites to improve the thermal and dielectric performance of polymer insulation for high voltage, high temperature electronics. However, using composite materials has been challenging due to manufacturing issues like incomplete mixing, inhomogeneous properties, and void formation. Here, NASA has developed a method of preparing and extruding polymer-ceramic composites that results in high-quality, flexible composite ribbons.
To achieve this, pellets of a thermoplastic (e.g., polyphenylsulfone or PPSU) are coated with an additive then mixed with particles of a ceramic (e.g., boron nitride or BN) as shown in the image below. After mixing the coated polymer with the ceramic particles, the blended material was processed into ribbons or films by twin-screw extrusion. The resulting ribbons are highly flexible, well-mixed, and void free, enabled by the coated additive and by using a particle mixture of micronized BN and nanoparticles of hexagonal BN (hBN).
The polymer-ceramic composite showed tunable dielectric and thermal properties depending on the exact processing method and composite makeup. Compared to the base polymer material, the composite ribbons showed comparable or improved dielectric properties and enhanced thermal conductivity, allowing the composite to be used as electrical insulation in high-power, high-temperature conditions.
The related patent is now available to license. Please note that NASA does not manufacturer products itself for commercial sale.
Materials and Coatings

Innovative Shape Memory Metal Matrix Composites
Shape memory alloys (SMAs) are metals that can return to their original shape following thermal input. They are commonly used as functional materials in sensors, actuators, clamping fixtures and release mechanisms across industries. SMAs can suffer from dimensional/thermal instability, creep, and/or low hardness, resulting in alloys with little to no work output in the long term. To combat these deficiencies, NASA has developed a process of incorporating nanoparticles of refractory materials (i.e., carbide, oxide, and nitride materials with high temperature resistance) into the alloys.
Using various processing methods, the nanoparticles can be effectively mixed and dispersed into the metal alloys as shown in the figure below. In these processes the SMA and refractory material powder is mixed and the refractory nanoparticles incorporated through extrusions, melting, or directly used in additive manufacturing to create parts for applications across the aerospace, automotive, marine, or biomedical sectors. The nanoparticle dispersion is a controllable method to strengthen the SMAs, increasing the hardness of the alloys, reducing the impact of creep, and improving the overall dimensional and thermal stability of the alloys.
The related patent is now available to license. Please note that NASA does not manufacture products itself for commercial sale.
materials and coatings
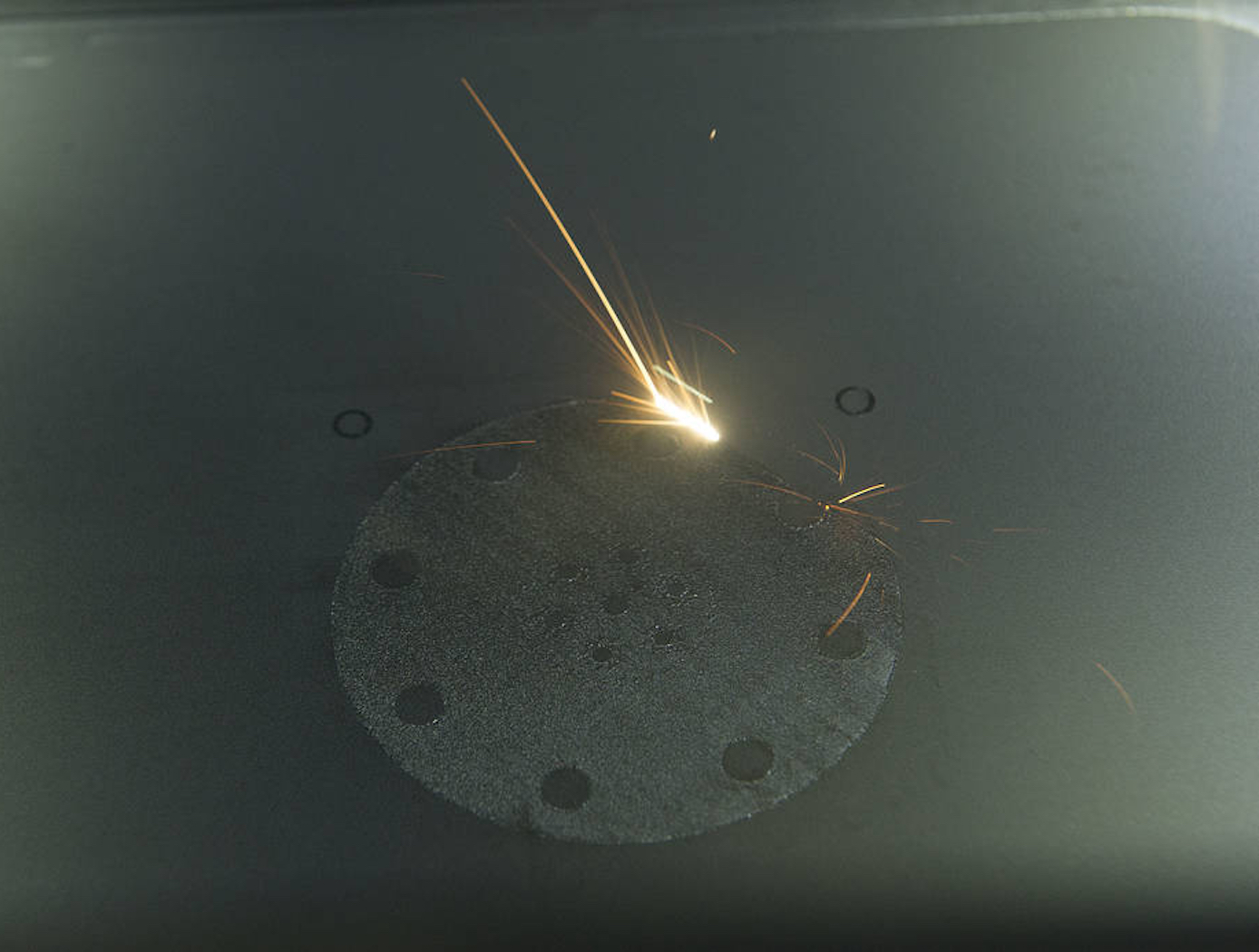
3D-Printed Composites for High Temperature Uses
NASA's technology is the first successful 3D-printing of high temperature carbon fiber filled thermoset polyimide composites. Selective Laser Sintering (SLS) of carbon-filled RTM370 is followed by post-curing to achieve higher temperature capability, resulting in a composite part with a glass transition temperature of 370 °C.
SLS typically uses thermoplastic polymeric powders and the resultant parts have a useful temperature range of 150-185 °C, while often being weaker compared to traditionally processed materials. Recently, higher temperature thermoplastics have been manufactured into 3D parts by high temperature SLS that requires a melting temperature of 380 °C, but the usable temperature range for these parts is still under 200 °C.
NASA's thermoset polyimide composites are melt-processable between 150-240 °C, allowing the use of regular SLS machines. The resultant parts are subsequently post-cured using multi-step cycles that slowly heat the material to slightly below its glass transition temperature, while avoiding dimensional change during the process. This invention will greatly benefit aerospace companies in the production of parts with complex geometry for engine components requiring over 300 °C applications, while having a wealth of other potential applications including, but not limited to, printing legacy parts for military aircraft and producing components for high performance electric cars.
manufacturing
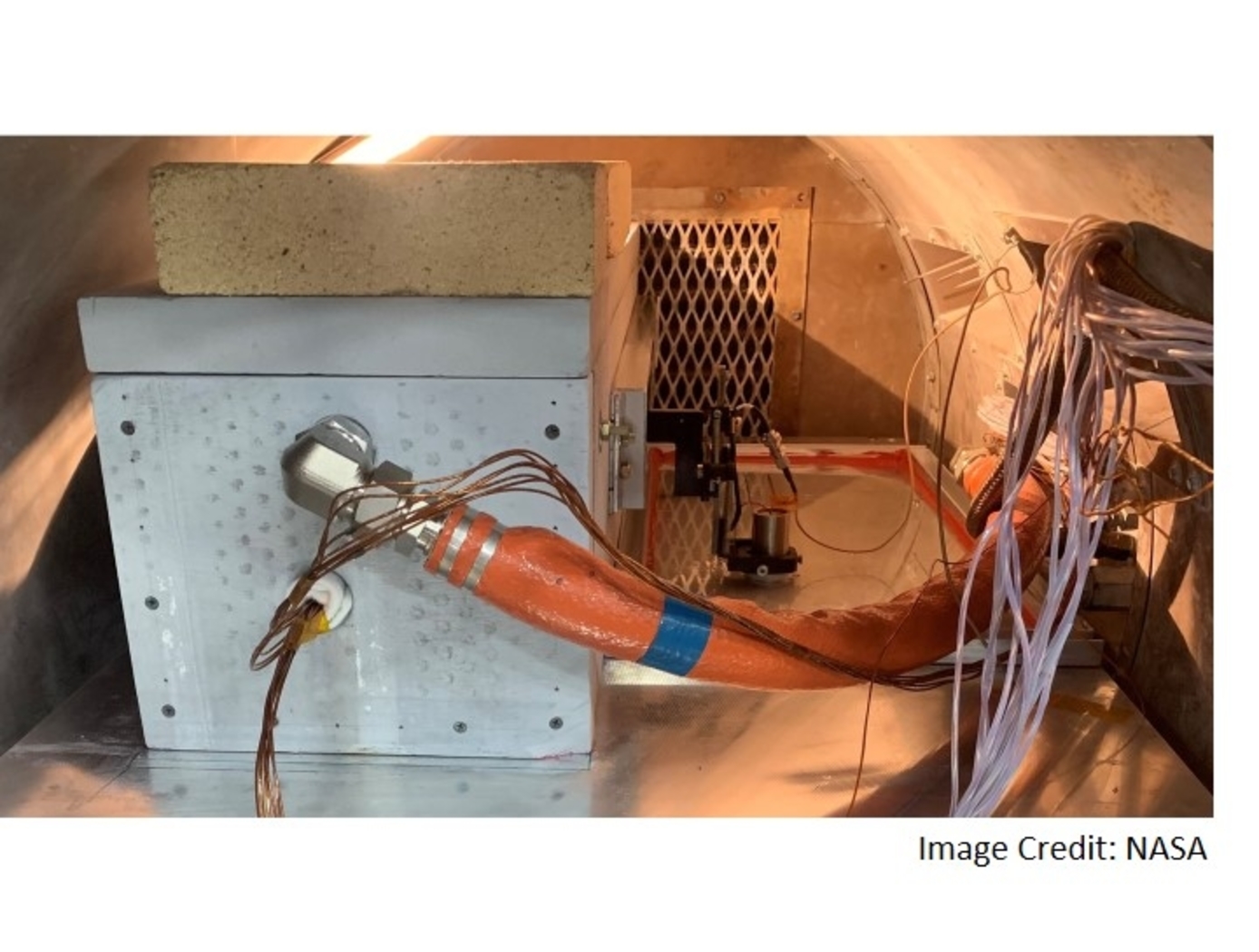
System for In-situ Defect Detection in Composites During Cure
NASA's System for In-situ Defect (e.g., porosity, fiber waviness) Detection in Composites During Cure consists of an ultrasonic portable automated C-Scan system with an attached ultrasonic contact probe. This scanner is placed inside of an insulated vessel that protects the temperature-sensitive components of the scanner. A liquid nitrogen cooling systems keeps the interior of the vessel below 38°C. A motorized X-Y raster scanner is mounted inside an unsealed cooling container made of porous insulation boards with a cantilever scanning arm protruding out of the cooling container through a slot. The cooling container that houses the X-Y raster scanner is periodically cooled using a liquid nitrogen (LN2) delivery system. Flexible bellows in the slot opening of the box minimize heat transfer between the box and the external autoclave environment. The box and scanning arm are located on a precision cast tool plate. A thin layer of ultrasonic couplant is placed between the transducer and the tool plate. The composite parts are vacuum bagged on the other side of the tool plate and inspected. The scanning system inside of the vessel is connected to the controller outside of the autoclave. The system can provide A-scan, B-scan, and C-scan images of the composite panel at multiple times during the cure process.
The in-situ system provides higher resolution data to find, characterize, and track defects during cure better than other cure monitoring techniques. In addition, this system also shows the through-thickness location of any composite manufacturing defects during cure with real-time localization and tracking. This has been demonstrated for both intentionally introduced porosity (i.e., trapped during layup) as well processing induced porosity (e.g., resulting from uneven pressure distribution on a part). The technology can be used as a non-destructive evaluation system when making composite parts in in an oven or an autoclave, including thermosets, thermoplastics, composite laminates, high-temperature resins, and ceramics.
materials and coatings
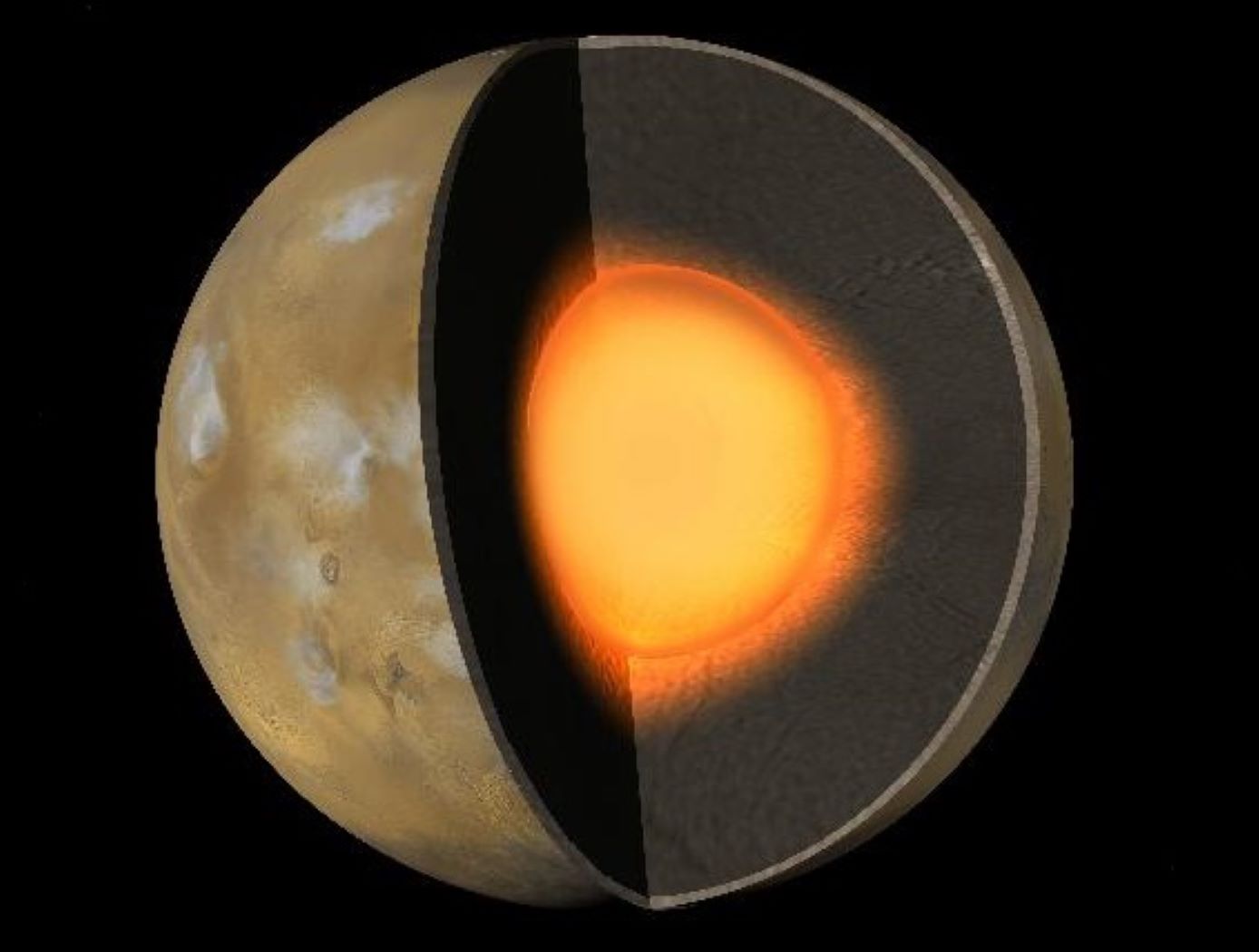
Diamond Maker Technology Simulates Alien Geology in Laboratories
Given the significant impact of fO2 on material properties, it is important to perform studies at fO2 values relevant to the sample of interest. However, current systems used to control fO2 in solid media assemblies (e.g., sliding sensors, graphite capsule buffering) have limited ability to produce the wide fO2 ranges necessary to simulate more extreme planetary interiors.
NASA's fO2 control system implements a modified double capsule design that utilizes a wide range of solid metal-oxide buffers to control fO2 across a wide range of conditions. The approach is a modification of the previous double capsule design wherein the outer capsule itself acts as the metal component of the buffer assemblage, and the inner capsule to which the astromaterial sample of interest is placed resides within the outer capsule.
To achieve higher experimental temperatures above the melting point of more traditional noble metal capsule materials, outer capsules of the control assembly are comprised of refractory (high melting point) metals such as Ni, Co, W, Fe, Mo, V, Cr, Nb and Ta. Resultant experiments have reliably achieved temperatures exceeding 1600 degrees C, and when used in conjunction with a multi-anvil press, system pressures of over 20 GPa can be obtained lending researchers the ability to simulate on or off-world geologic conditions previously difficult to obtain in a laboratory.
NASA's fO2 control system was developed to enable high pressure, high temperature experimental studies of astromaterials at fO2 values relevant to the sample of interest. However, it may also be useful for the synthesis of materials where fO2 control is required (e.g., synthesis of crystal structures that might be stable under higher oxygen pressure). Further use cases may include mineral or melt syntheses, metal-silicate or mineral-melt element partitioning, phase equilibria studies, and the possible development of new chemical and mineral compounds that could not be manufactured in laboratories before.
This fO2 control system technology is at a technology readiness level (TRL) 6 (system/subsystem prototype demonstration in a relevant environment). The innovation is now available for your company to license. Please note that NASA does not manufacture products itself for commercial sale.
manufacturing
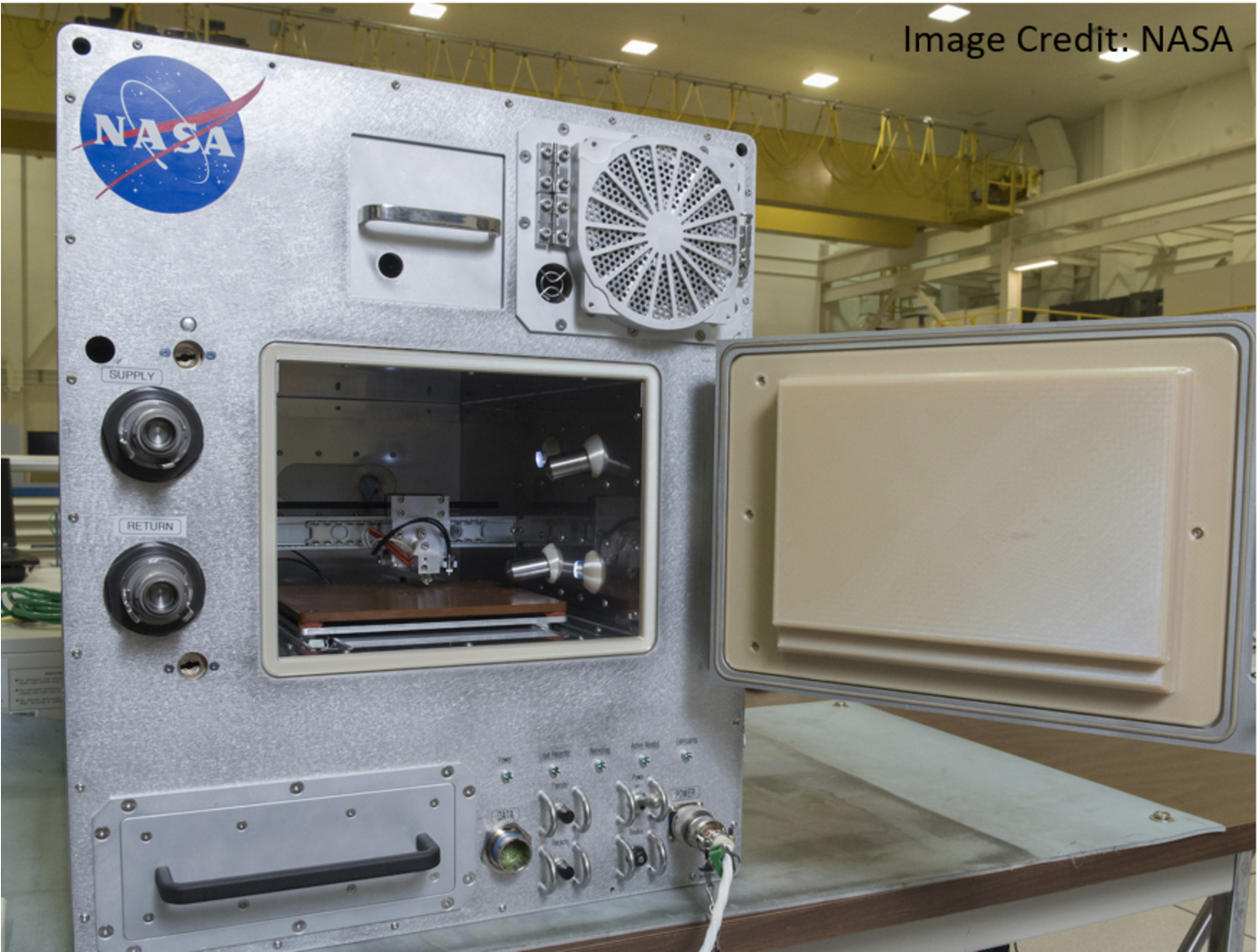
Recyclable Feedstocks for Additive Manufacturing
NASA's new technique for generating recyclable feedstocks for on-demand additive manufacturing employs the high-yield reversibility of the Diels-Alder reaction between maleimide and furan functionalities, utilizing the exceedingly favorable interaction between specific chemical functionalities, often termed "click reactions" due to their rapid rate and high efficiency. Integration of these moieties within a polymer coating on epoxy microparticle enables reversible assembly into macroscopic, free-standing articles. This click chemistry can be activated and reversed through the application of heat. Monomer species can be used to incorporate these functionalities into polyimide materials, which provide excellent mechanical, thermal, and electrical properties for space applications. Copoly (carbonate urethane) has been shown to be a viable coating material in the generation of polymer-coated epoxy microparticle systems and is amenable to being processed through a variety of approaches (e.g., filaments and slurries for 3D printing, compression molding, etc.). The polymeric materials are grown from the surfaces of in-house fabricated epoxy microparticles. The thermal and mechanical properties of the microparticles can be readily tuned by changes in composition.
There are a number of potential applications for this NASA technology ranging from use of these materials for recyclable/repurpose-able articles (structural, decorative, etc.) to simple children's toys. More demanding uses such as for replacement parts in complex industrial systems are also possible. For long term space missions, it is envisioned that these feedstocks would be integrated into secondary spacecraft structures such that no additional concerns would be introduced due to in-space chemical reactions and no additional mass would be required.
Materials and Coatings
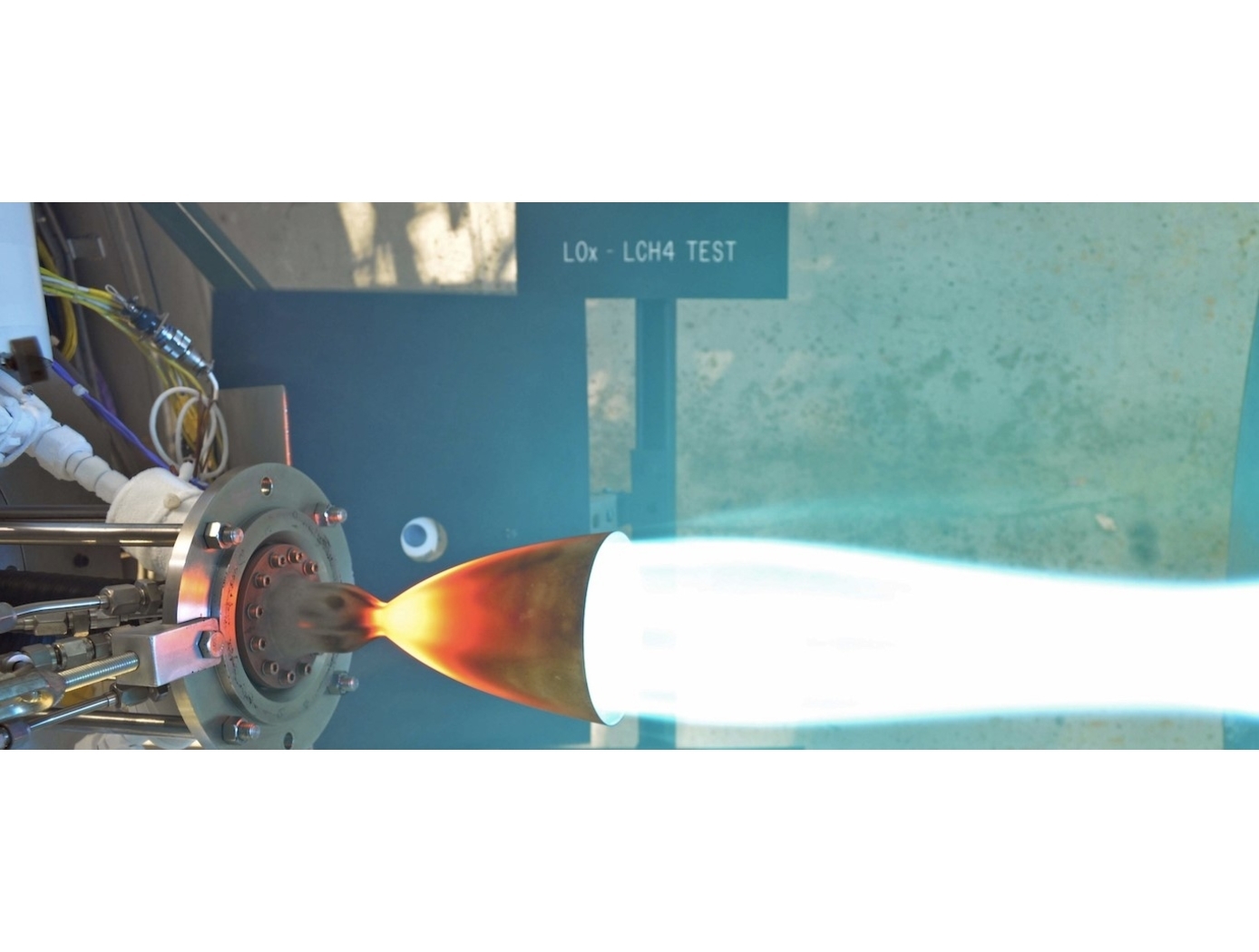
Oxide Dispersion Strengthened Medium Entropy Alloy
NASA's ODS-MEA maintains properties up to 1100°C and is not susceptible to deleterious phase changes when exposed to extreme temperatures, an issue ubiquitous to Ni- based superalloys such as Inconel-625 and Inconel-718. Yttria particles are dispersed throughout the alloy to maximize strength and creep resistance at high temperatures using a novel fabrication technique. This technique employs an acoustic mixer to stir nano-scale Yttria oxide powder within a metallic matrix powder, creating a film of Yttria surrounding the larger metallic powder particles. Solid components are then produced from this mixture via SLM, during which the laser disperses the Yttria particles throughout the microstructure. Ultimately, the process eliminates the many expensive and time-consuming steps in the production of ODS alloys via traditional mechanical alloying. NASA's process has been shown to fabricate components with 10x improvement in creep rupture life at 1100°C and provides a 30% increase in strength over what is currently possible with 3D printed parts. The new ODS-MEA composition may find applications where ODS alloys are currently used (e.g., those involving extreme thermal environments). Applications may also include areas where such properties are desirable but the resource-intensive nature and/or inability to produce highly complex geometries via conventional processes ultimately renders their use uneconomical or infeasible. Such uses include gas turbine components (for which increasing inlet temperature enables improved efficiency) for power generation, propulsion (rockets, jet engines, etc.), industrial processes, nuclear energy applications, and sample preparation equipment in the mining and cement production industries, among many others.